Wind Generation – What can EME do for ME?
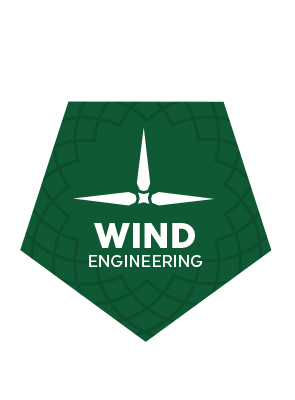
Wind generation has been a part of the US electricity supply since the early 1980’s and since that time, the contribution of wind power has continued to increase, currently accounting for approximately 6% of the total electricity produced. Although wind generators have been in-service for over 40 years, the generators are notorious for issues of reliability. EME excels at diagnosing the root cause of equipment failures and engineering solutions to address which can be implemented in-situ, saving the significant cost associated with having to bring in a crane to remove the generator from service. What can EME do for Wind owners and operators? – Develop creative and cost effective solutions to improve the capacity factor of your fleet or farm.
5 Key Factors About Wind
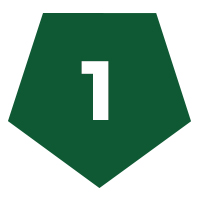
Wind power is rooted to the fundamental principles of converting mechanical energy to electrical energy that dates back to 19th century.
Where fossil and nuclear plants convert a fuel source into thermal energy and hydro converts the kinetic energy of flowing water into electric energy, a wind turbine converts the kinetic energy of wind into electrical energy. Common to all is harnessing this energy and delivery of the mechanical power to a shaft through torque and speed. This is then converted to electrical power through electromagnetics.
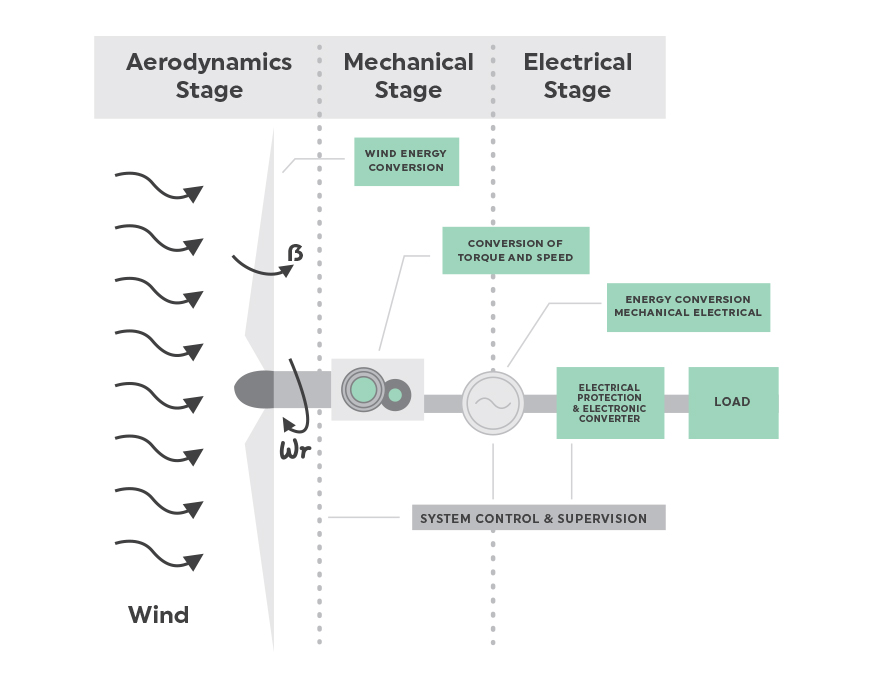
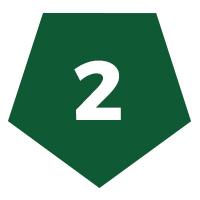
There are many types of generators in wind turbines:
- Fixed speed, induction generator
- Variable speed/slip, induction generator
- Variable speed, doubly fed induction generator (DFIG)
- Variable speed, fully rated converter (induction/synchronous/permanent magnet generators)
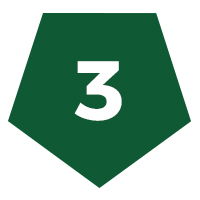
Key system and equipment in a doubly fed induction generator:
- Blades – convert kinetic energy of wind into mechanical work
- Pitch System – rotates the blade angle of attack with the wind velocity
- Yaw System – aligns the blades with the wind direction
- Gear Box – Transmits low speed high torque mechanical power from the blades to high speed lower torque mechanical power to the generator
- Generator – converts mechanical power to electrical power
- Inverter/Converter – delivers variable frequency AC to the rotor for 60 Hz electric power delivery to the grid
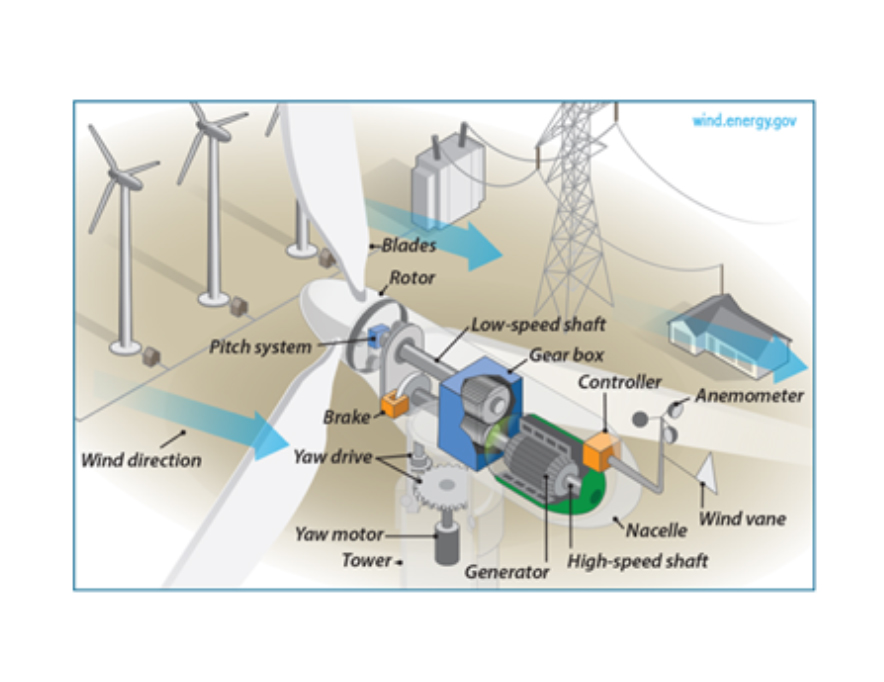
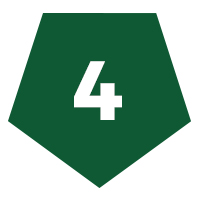
Key DFIG generator component maintenance and reliability issues:
- Stator winding failures
- Rotor winding failures
- Rotor connections (Wye Ring) failures
- Bearings failures
- Shaft voltages through parasitic capacitive coupling driving currents through the bearings
- Lubrication maintenance
- Vibration
- Excessive heating from slip rings
- Slip rings, brushes and brush rigging
- Magnetic wedges
- Cooling systems
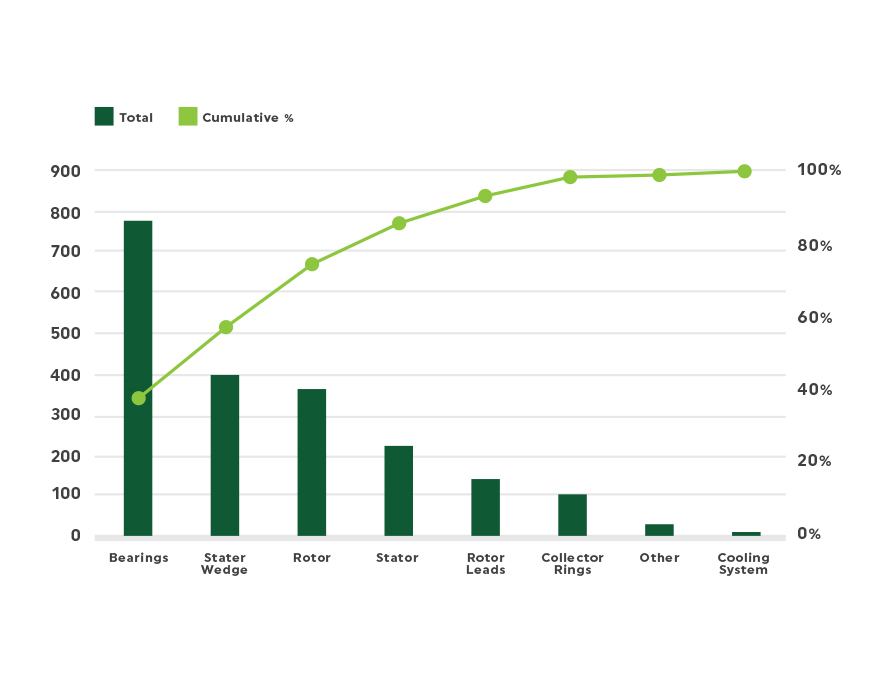
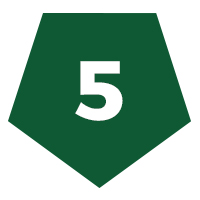
EME’s engineered solutions approach will deliver improved performance, reliability and cost savings through:
- Understanding equipment failures and their root causes and developing solutions that correct the problems and improve overall performance and reliability, not just a replacement or repair.
- Development of Maintenance and Maintenance programs that are well aligned with the equipment needs.
- Development of well-Coordinated Condition monitoring that delivers smart data to make informed decisions.
- Development of inspections and test methods and plans to work with condition monitoring to make condition and remaining life assessment evaluations