En
d-Turn and Phase Lead Vibration
Generator end baskets on large turbine generators present unique design challenges for generator manufactures and service organizations.
End baskets are comprised of individual end turns, which are integral to the end basket support structure through their arch binding with other structural components. This electrical and structural system made of relatively flexible members, must be designed to accommodate a large variety of functional requirements. For example the basket structure must be capable of handling the continuous electromagnetic forces at the forcing frequency (EFF) which is twice the electrical frequency.
The end basket structure and its components must also adequately attenuate the electromagnetic induced vibration and accommodate axial thermal expansion as a function of load and stop/starts. It must withstand thermal differential expansion forces within the basket structure itself, and it must be designed with sufficient rigidity and strength to handle fault and transient event forces without catastrophic damage.
When considering the electromagnetic forcing frequency (EFF) and maintaining end basket vibration levels within acceptable limits, it is extremely important that the end basket structures be designed void of natural modes at the EFF (120 and 100 Hz). This can prove to be a challenge to the designer as the EEF is a constraint in addition to the simple structural rigidity and thermal expansion requirements. An approach EME has used successfully is to combine impact test mode shape and natural frequency response data (modal parameters) with Finite Element Modeling and analysis.
This is a powerful methodology for analyzing persistent end vibration problems and in the development of effective repairs and modifications. The approach can be applied in a localized sense; correcting a resonant or highly responsive phase leads or lead, or it can be applied in the global sense to the overall basket structure in cases where it is resonant or highly responsive. In either case, operators should pay close attention to the natural frequencies of the end basket and phase leads, particularly post rewind to avoid degradation to the system, requiring implementation of extensive and costly repair work that adds to the regularly scheduled maintenance outages work scope.
Although this type of analytical effort is not always required, when necessary EME provides a truly independent source of the technical capabilities to study and correct end basket and phase lead vibration issues. Our extensive background in the methodology also ensures completion of the evaluation in the shortest time possible in order to get the correct upgrades implemented with the minimal impact to schedule.
Failure to adequately address the structural, thermal and EFF design constraints will result in excessive end winding vibration. Signs of end winding vibration; dusting (Photo 1) and greasing which forms between the end turns and the various blocking, support rings, bracket arms, etc. The dust, or grease when the dust mixes with oil, is the product of the wear that is taking place between the surface substrates due to relative vibratory motion. However, what can be of greater concern is the unseen damage below the coil insulation. This damage can include loosening and separation of strands that leads to break down of strand to strand insulation and high cycle fatigue and potential breakage of strands (Photo 2).
Other serious and catastrophic damage includes high cycle fatigue breakage of series connectors, phase leads, and phase lead connectors (Photo 3/4).
To get more detail, please contact Tom Cunningham at tcunningharm@emeassociates.com
Photo 1 – Dusting in Large Air Cooled Generator resulting from End Basket Vibration

Photo 2 – Direct Hydrogen Cooled Stator Winding Failure Resulting from Strand Breakage
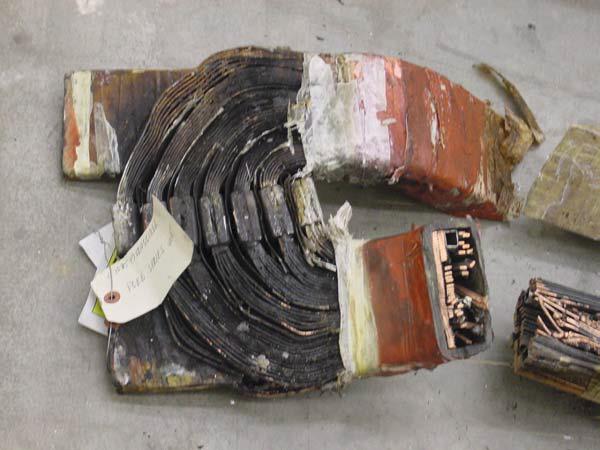
Photo 3 – High Cycle Fatigue Crack Phase Lead Connector
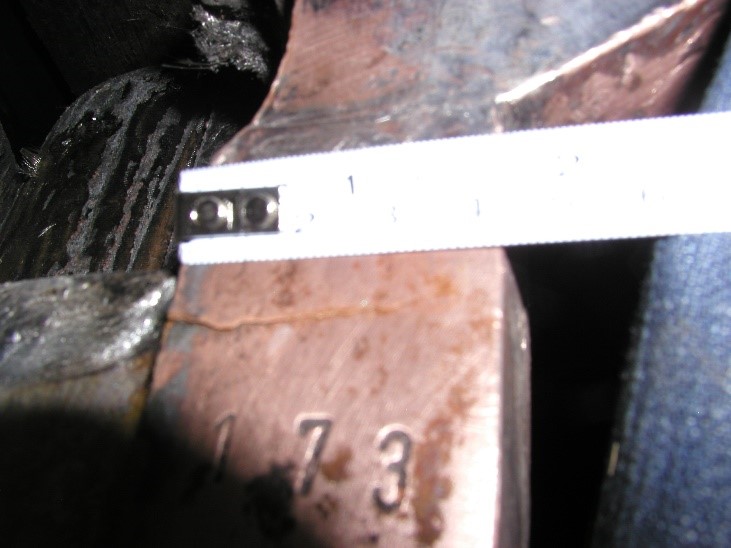
Photo 4 – Phase Lead Connector Failure
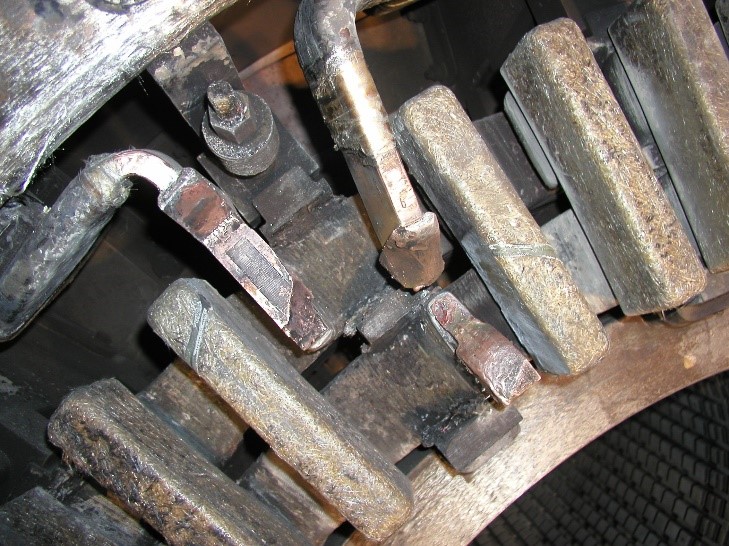